
RTG design, construct and install pellet production lines for our customers. They range in size from 200kg/hr to 20Tonnes/hr. Project management of the turnkey project in collaboration with our European partners is the backbone of our business. RTG chose to use Nova pellet machinery for pellet systems <1.5 Tph and CPM of Europe for systems >1.5Tph. We can design a complete system from fibre handling, wet grinding, drying, material storage, dry milling, pelletising, cooling and storage of finished pellets ready for bulk loading into trucks/trains to take to port.
RTG also has a pellet line in their factory where pellets are produced every day for distribution to customers with pellet consuming devices such as hot water units and heaters. We can also run test trials for prospecting customers to determine pellet suitability. We can also supply test results for pellet density, calorific value, trace elements, ash content and ash fusion temperature.

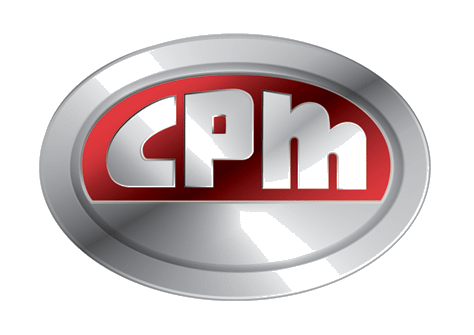

RTG are leaders in designing and installing turnkey pellet press solutions. Working in conjunction with Nova Pellet, Italy’s number one pellet equipment manufacturer, and CPM Europe, we are able to tailor a solution to meet your specific waste needs. With the growing trend of manufacturers and businesses becoming more environmentally responsible coupled with the increasing cost of waste removal, now is the perfect time to consider a pellet press solution for your business. A pellet press will allow you to utilise your biomass and waste by turning it into Wood Pellets.
What are Wood Pellets?
Wood pellets are a natural, high energy fuel source that can be used to fuel pellet heaters and as a substitute fuel source for boilers. High quality wood pellets are always in demand and with the growing Pellet Heater market in Australia now is the perfect time to turn your waste into profit. Installing a pellet press will reduce both your waste removal and disposal costs as well as your carbon footprint.
What is Pelletising?
Pelletising is the process of drying, shredding and compressing wood off cuts, saw dust, shavings and biomass into high energy wood pellets. These pellets can then be used or packaged and resold as a premium product.
Customer Testing:
RTG have set up a pellet production line in their factory. This will be used to produce premium wood pellets for the Australian market as well as provide a facility for customers to test their waste. To adequately test waste we require a minimum of 0.5-1m³ of raw material. Moisture content of raw material needs to be between 9-11%.
RTG are able to provide full turnkey installations including:
-
Storage Silos
-
Hammer Mill
-
Conditioning Silo
-
Pellet Mills
-
Cooling Tower
-
Screw Conveyors
-
Packaging Line
Why Choose Nova?
Nova Pellet are the No. 1 pellet equipment manufacturers in Italy. They have been supplying manufacturers globally with pellet production solutions for many years and are extremely knowledgeable and experienced in the field. Nova Pellet manufacture the highest quality machinery to ensure you achieve the highest quality wood pellets. Recycling Technologies Group have the ability to provide you with a turnkey Nova Pellet solution, completely tailored to suit your individual needs.
Raw Materials
Pellets can be made from the following waste:
-
Saw dust
-
Shavings
-
Wood off cuts
-
Certain types of paper and cardboard
-
Various other types of biomass
Moisture Content
-
Moisture content of the finished pellets is between 8.5 and 10%. Raw material feed stock should be less than 10%. However, because raw material dries out during the shredding and hammer milling process, sometimes we can use raw material with a moisture content of up to10.5%
Australian Standards
-
Australian Standards (4014.6) states that pellets need to have a density of at least 640kg/m³. However, our experience has shown that softwood pine pellets should be around 680kg/m³ and we can achieve in excess of 750kg/m³ with hardwood. These higher densities result in less fines, longer pellets and less breakage in transport.
-
We are able to achieve this due to the superior design of the European die sets.
The Dies
-
The type of dies used in pelletising is one of the most important aspects in making premium pellets. The ring die must have excellent machining accuracy and metallurgical wear characteristics.
-
Accurate machining is critical to ensure a precisely controlled gap between the roller shells and the inner dies surface
Conditioning
-
Premium pellets need to be conditioned after hammer milling and prior to pelletising to ensure the correct moisture content. Both Nova and CPM machinery have this cooling feature built into their design